On April 16, at the AICE 2025 SMM (20th) Aluminum Industry Conference and Aluminum Industry Expo—Aluminum Casting Technology Forum, co-hosted by SMM Information & Technology Co., Ltd., SMM Metal Trading Center, and Shandong Aisi Information Technology Co., Ltd., and co-organized by Zhongyifeng Jinyi (Suzhou) Technology Co., Ltd. and Lezhi County Qianrun Investment Service Co., Ltd., a certified expert from the China Nonferrous Metals Think Tank and the chief engineer and senior engineer of Anhui Guangsheng Meichen New Materials Technology Co., Ltd. shared insights on safety hazards in aluminum processing and the dual prevention mechanism.
1. Preface
The theme revolves around "Everyone Talks About Safety, Everyone Knows Emergency Response—Smooth Life Channels," emphasizing the importance of safety first, prevention as the priority, and comprehensive management. The focus is on addressing both symptoms and root causes, with a particular emphasis on reducing major safety risks and eliminating significant accident hazards.
2. National Requirements
The expert elaborated on how the "dual prevention mechanism" was proposed. The newly revised "Work Safety Law of the People's Republic of China" added provisions for establishing a dual prevention mechanism for safety risk classification control and hidden danger investigation and management. The main purpose is to implement the safety work requirements of the Party Central Committee and the State Council, ensuring that safety risk control precedes hidden danger management and that hidden danger investigation and management precede accidents. This aims to enable production and operation units to identify and control safety risks independently and manage hidden dangers autonomously. The key is to effectively carry out hidden danger investigation and management, preventing and resolving major safety risks at the source and addressing issues before they escalate.
Why was the "dual prevention mechanism" proposed?
Recent major accidents have exposed significant issues in the field of work safety, such as "unclear understanding and unforeseen problems." In response, General Secretary Xi Jinping has repeatedly emphasized the need to anticipate new situations and unforeseen problems in industries prone to major accidents. The shift from hidden danger investigation and management to safety risk control requires strengthening risk awareness, analyzing the entire chain of accident occurrence, and taking preventive measures at key links to prevent safety risk control failures from turning into hidden dangers and hidden dangers from evolving into accidents.
3. Detailed Explanation of Dual Prevention
Dual prevention refers to the dual prevention mechanism of safety risk classification control and hidden danger investigation and management. This mechanism is the foundation and important guarantee of enterprise safety management. Below is a detailed explanation of dual prevention:
1. Safety Risk Classification Control
Safety risk classification control is the first line of defense in the dual prevention mechanism. Its main contents include:
a. Risk Identification: Identifying hazardous substances and energy at risk points and the conditions under which these may cause accidents.
b. Risk Assessment and Classification: Using risk assessment criteria to evaluate identified risks and classifying them into different levels, such as extremely high, high, medium, and general safety risks (typically corresponding to red, orange, yellow, and blue labels).
c. Risk Control: Ensuring that safety control measures at risk points are effective and managed by personnel at different levels.
2. Hidden Danger Investigation and Management
Hidden danger investigation and management is the second line of defense in the dual prevention mechanism. Its main contents include:
a. Hidden Danger Investigation: Conducting comprehensive inspections of control measures at risk points to promptly identify potential hidden dangers.
b. Hidden Danger Management: Timely management of identified hidden dangers to prevent them from escalating into accidents. Management requires the implementation of "five guarantees": responsibility, measures, funds, timelines, and contingency plans.
3. Purpose and Significance of the Dual Prevention Mechanism
The purpose of establishing the dual prevention mechanism is to address prominent issues in work safety, emphasizing the shift from hidden danger investigation and management to safety risk control. This mechanism helps enterprises fully implement their main responsibility for work safety, improve the effectiveness of accident and disaster prevention, reduce losses from accidents and disasters, and promote social stability and economic development. Additionally, the dual prevention mechanism emphasizes strict control over two key aspects: risk control, focusing on major risks, and hidden danger management, ensuring timely management of major hidden dangers. Through the dual prevention mechanism, every type of risk is controlled within acceptable limits, every hidden danger is managed at its inception, and every accident is eliminated in its early stages.
In summary, the dual prevention mechanism is an essential component of enterprise safety management. It emphasizes starting with risk identification, using risk control as a means to prevent risks from turning into hidden dangers, and ensuring enterprise safety through hidden danger investigation and management.
4. Main Examples of Aluminum Processing Hazards
1. Focus on key areas of safety prevention. Highlight safety supervision of high-risk operations such as melting furnaces, deep well casting, dust explosion, and confined space operations. Conduct in-depth analysis of the jurisdiction, target efforts, overcome difficulties, and resolutely prevent and control major and above accidents. Urge enterprises to study and formulate practical safety management measures based on their characteristics and strictly implement them to reduce sporadic accidents.
2. Melting Furnace Area:
3. Casting Area:
③ Equipment: 1. Three emergencies: a. Trough (furnace) emergency pool, b. Emergency power supply, c. Emergency water;
④ Two liquid level controls + discharge: 1. Liquid level control and discharge from the furnace outlet to the online device trough, a. Discharge back to the furnace, b. Discharge to the trough emergency pool (tank);
2. Liquid level discharge from the trough to the water pan trough, a. Cut-off valve for the water pan and b. Trough discharge valve "automatically synchronized" discharge to the trough emergency tank;
5. Management Measures
1. Promote the dual prevention mechanism of risk classification control and hidden danger investigation and management. Encourage employees to voluntarily and dynamically report hidden dangers in a timely manner, effectively enhancing the enterprise's proactive management vitality.
① Establish and improve the work safety responsibility system: Clarify the work safety responsibilities of leaders at all levels, various departments, and positions, sign work safety responsibility letters at all levels, and form a work safety responsibility system that extends horizontally and vertically.
② Establish a work safety leadership group headed by the main responsible person, hold regular work safety meetings (at least once a month), and ensure effective progress in work safety.
③ Improve work safety management systems, operating procedures, and emergency plans based on the actual situation of the unit, ensuring that all systems comply with legal and regulatory requirements and are operational and targeted.
④ Ensure the effective implementation of various work safety systems through daily inspections, special inspections, and random (monitoring) inspections, and deal seriously with violations of the systems to form effective constraints.
⑤ Organize all employees to participate in training on work safety laws and regulations, operating procedures, emergency rescue, etc., and ensure that new employees (pre-job training, three-level safety training education) have completed the training to improve employees' safety awareness and operational skills.
⑥ Ensure that employees are certified and strictly follow operating procedures to prevent accidents.
⑦ Improve emergency plans based on the actual situation of the unit, clarify emergency response procedures, rescue measures, and guarantee measures, and improve the pertinence and operability of emergency plans.
⑧ Develop a hidden danger investigation and management plan, clarify the content, methods, and frequency of investigations, and ensure comprehensive and in-depth hidden danger investigation work; register identified hidden dangers, formulate rectification measures, and ensure timely rectification of hidden dangers.
2. Four Enhancements in Hidden Danger Investigation
① Enhance hierarchical investigation and control: The main responsible person of the production and operation unit is fully responsible for the investigation and management of hidden dangers. Enterprises should establish a four-level self-inspection and self-correction mechanism at the post, team, workshop, and factory levels according to the dual prevention system; team, workshop, and company leaders and managers, as well as post operators, should adhere to daily work safety inspections; the main responsible person of the unit should organize at least one hidden danger investigation per month involving safety management personnel, engineering and technical personnel, production supervisors, and employees. Improve the hidden danger investigation and management mechanism of "enterprise self-inspection and self-correction, expert guidance inspection, superior safety department supervision and inspection, and law enforcement supervision and rectification." Only through hierarchical investigation can the dual prevention system be effectively implemented.
② Enhance the "Four Hundreds": Hidden danger investigation should achieve 100% in time: adhere to full-time, ensure 24-hour on-duty investigation, and employees should investigate hidden dangers for 60 seconds while on duty for one minute; hidden danger investigation should achieve 100% in personnel participation (full participation): urge employees to firmly establish the safety concept of "not harming oneself, not harming others, not being harmed by others, and protecting others from harm"; hidden danger investigation should achieve 100% in key parts and critical links: adhere to comprehensive and thorough investigation, leaving no aspect uncovered; hidden danger investigation should achieve 100% in all departments of the enterprise: investigate hidden dangers according to the systematic method, differentiate different objects and departments for comprehensive investigation, and especially strengthen hidden danger investigation for external construction units, new employees, and visitors.
③ Enhance hierarchical management: Register identified hidden dangers according to their level, establish a hidden danger information file, and implement monitoring and management according to the division of responsibilities. If safety cannot be guaranteed before or during the elimination of hidden dangers, take emergency preventive measures or special protective measures, and if necessary, stop production, evacuate personnel, and suspend business for rectification.
Each production and operation unit should strictly implement the principle of "lower-level management of hidden danger management measures" for identified hidden dangers: team leaders should personally handle team hidden dangers, workshop directors should personally handle workshop hidden dangers, and general managers should personally handle factory-level hidden dangers. At the same time, strictly implement the principle of "upper-level responsibility for hidden danger management": if hidden dangers lead to accidents, the responsibility should be traced to the upper level. This is the essence of "hierarchical management."
④ Enhance the "Two Regulars": Regularly have people interviewed or punished for safety issues; regularly have people commended for good performance in work safety. This is the "Two Regulars." Increase the weight and intensity of work safety in the performance evaluation of enterprise leaders at all levels, and incorporate work safety, especially hidden danger investigation and management, into the overall goals of enterprise production and operation. Further improve the work safety reward and punishment system, appropriately commend and reward departments and individuals with significant achievements, and strictly hold accountable those who violate laws and regulations or fail to act. At the same time, focus on strengthening work safety emergency management, emergency plans, and emergency drills, improve the emergency plan system, and ensure the filing of enterprise work safety rescue plans, regularly organize plan drills to improve the enterprise's self-rescue capability.
⑤ Deep well casting operation process, achieve "five-point linkage," and prevent molten aluminum from entering the casting well and encountering water to cause hidden dangers.
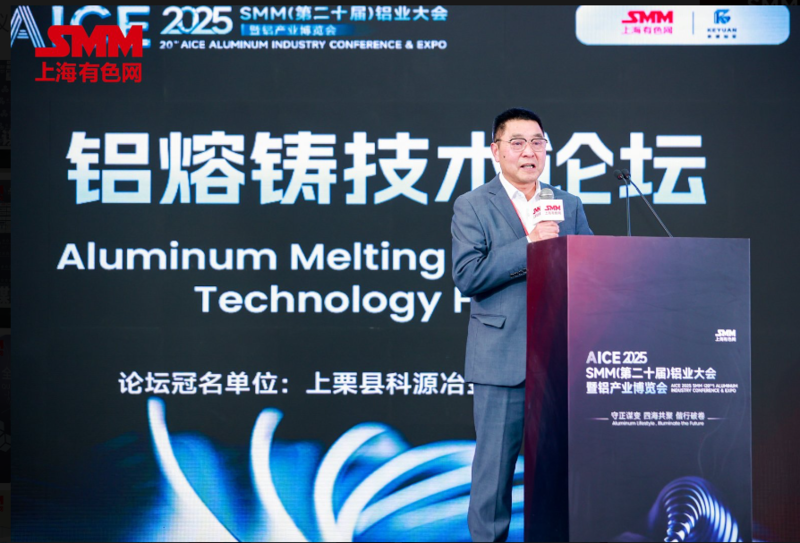


First Point: The outlet liquid level control linkage of the holding furnace (also known as the stationary furnace, including the integrated melting and holding furnace, which refers to the furnace group connected to the casting machine, the same hereinafter). During the casting process (usually after the initial 300-500 mm and before the end), when the outlet liquid level of the holding furnace suddenly rises or is extremely high, or suddenly drops or is extremely low, the supply flow trough gate is cut off, the discharge gate is opened, or the lifting device at the entrance of the distribution trough is disconnected to stop the flow, and the tilting furnace automatically tilts back.
Second Point: The liquid level control linkage between the main supply trough and the casting plate or the entrance of the distribution trough (core clause). During the casting process (usually after the initial 300-500 mm and before the end), when the liquid level of the main supply trough and the casting plate (mold plate) or the entrance of the distribution trough suddenly rises or is extremely high, or suddenly drops or is extremely low (the core of the core), the main supply trough gate is cut off, the discharge gate is opened, or the lifting device at the entrance of the distribution trough is disconnected to stop the flow, and the tilting furnace automatically tilts back.
Third Point: The cooling water flow, pressure, and temperature control linkage of the casting plate or crystalliser. After the casting starts normally, when the cooling water pressure and flow of the casting plate (mold plate) or crystalliser suddenly drop, the main supply trough gate is cut off, the discharge gate is opened, or the lifting device at the entrance of the distribution trough is disconnected to stop the flow, the tilting furnace automatically tilts back, and the cooling water temperature is monitored.
Fourth Point: The sudden power and water outage linkage of the casting machine. During the casting process, when the casting machine suddenly loses power or water, the main supply trough gate is cut off, the discharge gate is opened, and emergency water is activated; when the power is out, the emergency power supply (seamless) is activated, the main supply trough gate is cut off, the discharge gate is opened, or the lifting device at the entrance of the distribution trough is disconnected to stop the flow, and the tilting furnace automatically tilts back. Fifth Point: The sudden rise in water temperature at the outlet (return water) of the casting well linkage. During the casting process, when the water temperature at the outlet (return water) of the casting well rises suddenly in a short time, the main supply trough gate is cut off, the discharge gate is opened, or the lifting device at the entrance of the distribution trough is disconnected to stop the flow, and the tilting furnace automatically tilts back. In emergency situations, through the "five-point linkage," the continuous flow of molten aluminum to the casting plate or distribution trough can be blocked or delayed, thereby preventing the molten aluminum from entering the casting well and causing a potential accident of molten aluminum encountering water.
Employees who are familiar with and perform the above tasks well will basically avoid potential hazards.
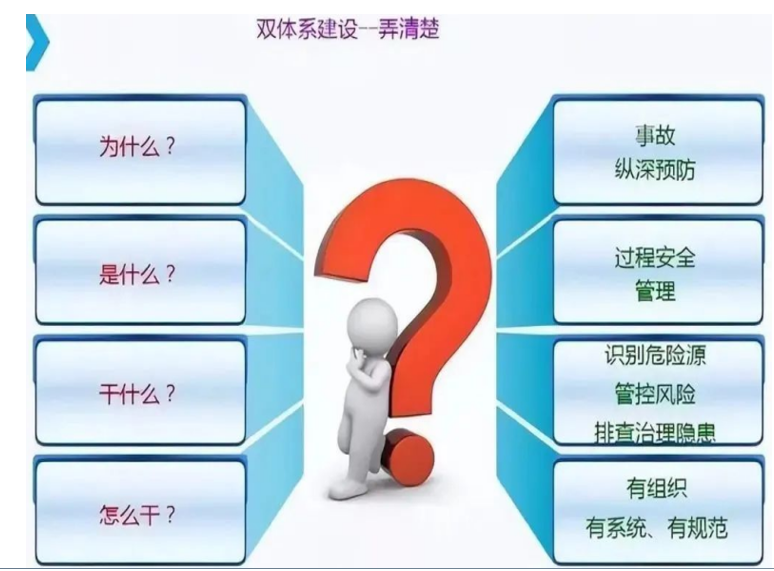
6. Conclusion
In summary, by strengthening organization, hazard investigation and management, regulatory enforcement, enhancing process control, improving technical support, intelligent control, and third-party professional service guarantee measures, by building a hazard investigation and management system and a closed-loop management system, timely discovering and eliminating various accident hazards, deepening hazard management, and a series of measures, risk control and hazard management are in place; safety production work is a long-term and arduous task, we will continue to fulfill our safety production responsibilities with a high sense of responsibility and mission, constantly summarize experiences and lessons, improve safety production systems, strengthen safety production management, maintain our original aspiration and take on our mission, strengthen confidence and act bravely, prevent problems before they occur, and ensure the long-term stability of the company's production and business activities; the journey is long and the wind is strong, the heavy responsibility is upon us again.
》Click to view the AICE 2025 SMM (20th) Aluminum Industry Conference and Aluminum Industry Expo Special Report